Boiling
Boiling is considered when the temperature of the fluid film is above the boiling temperature. Below the boiling temperature, the same equilibrium conditions as for evaporation are assumed, but the vapor mass rates are determined differently.
There are two distinct choices for modeling fluid film boiling in Simcenter STAR-CCM+, namely the Rohsenow and the Habchi Boiling models.
Rohsenow Boiling
The empirical standard pool boiling
correlation [632] is used to model liquid film boiling at a hot wall. The film
starts to boil when the wall temperature exceeds the boiling temperature of the
liquid. The heat flux passing from the wall to the film increases in proportion to
the cubic power of
where:
- the viscosity
, the Prandtl number , and the specific heat are evaluated for the liquid phase. -
and denote the densities of the liquid and gas phases. -
and denote the gravity acceleration and surface tension coefficient respectively. -
and characterize the fluid wall interface.For example, for water-brass contact, the values are
and . -
represents the saturation temperature of the mixture and is computed from the temperature-dependent saturation pressure of its components by applying Dalton’s law.
The heat flux increases as
where
where
The wall temperature of maximal heat
flux
Based on this correlation, the heat flux from the wall is computed as follows:
The component mass rates of vaporization are then computed as
where
- when heat is supplied near the wall to bubbles which then move away into the liquid film and condense into the film
- when evaporation takes place at the base of a bubble and condenses at its tip.
- Bulk Boiling
- The heat transfer to the interface between
the phases is used to compute the rate of evaporation.
For the Rohsenow boiling model, Simcenter STAR-CCM+ calculates the mass rate of evaporation from:
(2808)assuming that:- The vapor bubbles are at the saturation temperature.
- The temperature of the liquid is approximately the temperature of the mixture.
- All the heat flux from the liquid to the interface is used in mass transfer due to evaporation.
is the product of the heat transfer coefficient between the vapor bubbles and the surrounding liquid, and the specific contact area (contact area per unit volume) between the two. is the latent heat of vaporization of the mixture:(2809)where
is the mass fraction and is the latent heat of pure component . This latent heat is the difference between the enthalpy of its liquid phase and its gas phase .(2810)
Habchi Boiling
The Habchi boiling model calculates the vaporization of liquid films across both nucleate and transition boiling regimes. Additionally, the Habchi boiling model considers the effects of ambient gas pressure and wall roughness when calculating the liquid evaporation rate.
The Habchi boiling approach uses the saturation, Nukiyama, and Leidenfrost temperatures to differentiate between the fluid film boiling regimes.
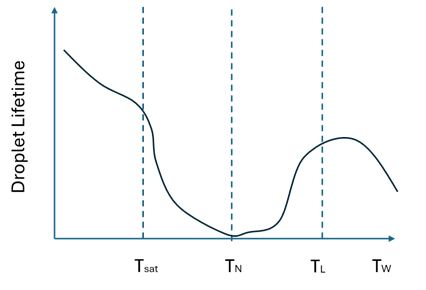
- Below the saturation (boiling) temperature, when
, the heat flux is low, and evaporation occurs to some extent. - When
, vapor cavities form around nucleation sites on the wall. The maximum heat flux is reached at the Nukiyama temperature . - For
, above the Nukiyama temperature, vapor pockets coalesce to form a cushion, which reduces the contact of the liquid with the wall, thus slowing conduction. - When
, in the Leidenfrost regime, the presence of the vapor cushion further slows conduction.
At high wall temperatures, the
film rapidly heats up and boils away. As a result, when the film thickness
approaches zero, Simcenter STAR-CCM+ limits the
maximum film temperature to the wall temperature to ensure that a defined zero
thickness film behaves as if there was no film. If any film remains and boiling
occurs, the film temperature remains below
The thermal
boundary height can be calculated by using the maximum evaporation rate
where:
-
-
is the vapor thermal conductivity. -
is the thickness of the vapor cushion.
-
is the dry fraction of liquid film area due to boiling, and is calculated as:(2819) -
is the dry fraction of liquid film value at the Leidenfrost point. This value is 0.98 . -
is the dry area fraction coefficient which sets the strength of the boiling rate through the vapor cushion. The default value of 0.055 is based on iso-octane. -
is computed from:(2820)
and:
-
is the film thickness. -
is the contact angle. -
is the maximum length of the contact lines of the liquid film. -
is a dimensionless length density of contact lines, defined as:(2822)and . -
is the minimum dimensionless length density of contact lines.
-
and are adjustable constants of the model. The default values are 1.0 and 0.2, respectively. -
is the average roughness of the wall (height is assumed).
Nukiyama and Leidenfrost Temperature
where:
-
is the critical temperature. For multi-component liquid this is the highest of the critical temperatures of the liquid components. -
is pressure. -
is . -
is the normal boiling temperature at 1 atm. For a multi-component liquid, choose as a function of composition.
If there are no experimental data available, the Nukiyama temperature is estimated it to be halfway between the film saturation temperature and the Leidenfrost temperature: