Particle Clustering and Breakup
Particle bonding is used to extend the particle model to more complex (compliant) shapes or structures. You use the particle clumps model to create groups of particles that represent a complex shape. The particle clumps model invokes the bonded particles model where the individual particles retain their separate identities and are linked by elastically compliant bonds, to each other or to a wall. The addition of a damage model allows the fracture and fragmentation of the clump with the constituent particles separating from the clump.
The composite particle model, on the other hand, treats the ensemble as a single rigid body that does not separate during the simulation.
Particle agglomeration use the same mechanism as the clumped particles, however the bonds are formed in an interval during the simulation as particles collide or according to a user-given criterion. This forming of bonds can be part of an initialization phase where, for example, particles are packed into a volume and an initial configuration is formed. The mechanism is also used to represent a process, for example, a tableting process during the simulation. The result is to form a compliant structure with damage as an option.
Particle Bonding Model
The particle bonding model is used by both the particle agglomeration model and the bonded particle (clumps) model. The particle agglomeration model uses particle bonding to describe interactions between the constituent particles, but also models elastic collisions between particles, based on the elastic contact models chosen by the user. The bonded particle (clumps) model uses only the particle bonding model.
The particle bonding model simulates cumulative damage to bonds. When an interaction producing some damage but falls short of failure, the amount of that damage is reflected in the reduced strength of the bond.
The parallel bond forces are represented in the following governing equations [730].
Force and torque on a particle due to parallel bonds is:
where the terms
where:
where
where
The parallel bond can be treated as brittle and disintegrative when shear and tensile stresses exceed prescribed limit values. The stress limit values are calculated based on beam theory to be:
where:
|
maximum tensile stress that is calculated in the bond |
|
maximum shear stress that is calculated in the bond |
If either value exceeds the predefined maximum, the bond is removed and the forces are further calculated only based on the granular interaction of particles.
Simple Failure Model
The simple failure model breaks a bond
in the simulation if tensile stress or shear stress on the bond exceed one of the
user-specified maximum values
where:
-
is the maximum tensile stress that is allowed without failure of the bond . -
is the maximum shear stress that is allowed without failure of the bond .
Impact Cutting Model
The impact cutting model breaks a bond
in the simulation if the particle impact velocity magnitude
For a particle with multiple bonds, only one bond can break at a time if more than one fiber segment or pair of clumped spheres satisfies the breakage criterion. In this situation, the breaking bond is the one closest to the impact position. For the two end segments, only one bond exists though.
Secondary breakage can occur after the time from the previous breakage exceeds the user-specified Breakage Time Interval.
The model determines which bond breaks using the following steps:
- Identify the segment with the maximum impact velocity magnitude
that exceeds
:with:
where:
-
is the maximum impact velocity magnitude among all segments of a fiber or spheres of a clumped particle. -
is the number of bonded components of a bonded particle.
-
- For secondary breakage, check if
where:
-
is the time of the previous breakage. -
is the user-specified Breakage Time Interval.
-
- Let
and be the two bonds associated with the segment, and be their bond locations, and be the impact position. Then the bond to break is if , or otherwise.
Constant Rate Damage Model
The constant rate damage model simulates the weakening and breaking of bonds between particles in a clump due to collisions.
The constant rate damage model follows the stress-strain curve shown in the following figure:
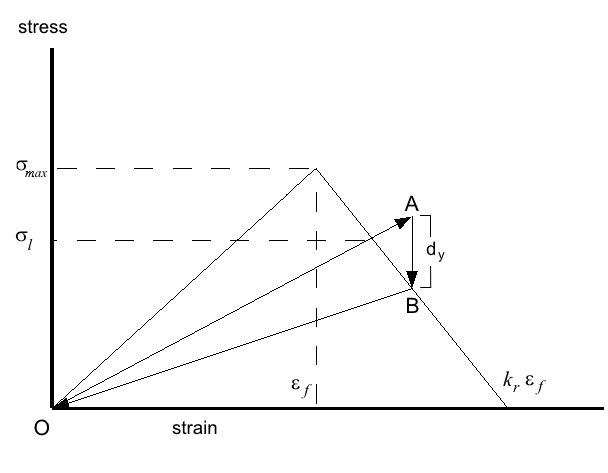
The point (
If
where:
is the Rayleigh wave speed. is the bond radius. is the size of the time-step.
where:
The maximum tensile stress for the bond is calculated as:
-
is the calculated value of the locally maximum tensile stress within the bond. See Eqn. (3292). -
is the calculated value of the locally maximum shear stress within the bond. See Eqn. (3293).
If
As a bond is damaged, its stiffness is modified. When the bond is in tension, the stiffness of the bond, which is represented by the parameters
When the bond is in compression, no reduction of stiffness occurs, because the direct contact of a fracture surface transmits the normal load. The resultant friction together with surface asperities work to transmit the shear force.