The imposed stretch spark ignition model (ISSIM) is a Eulerian spark-ignition
model for 3D RANS simulations of internal combustion engines.
The spherical kernel equation is used directly in the Eulerian transport
equations—allowing a description of all local phenomena. The use of a flame surface
density equation allows the simulation of multi-spark ignition and of the flame holder
effect. Both flame growth and wrinkling are modelled via the ECFM equation.
Assuming an inductive ignition system, the ISSIM model provides the amount of energy
transferred to the gas during the glow phase as well as the evolution of the spark,
which is then convected and wrinkled by the flow. At the instant of electrical
breakdown, an initial burnt gas profile is created on the 3D CFD mesh. From then on, the
reaction rate is directly controlled by the flame surface density (FSD) equation. A
number of adjustments are then made to this equation so that it can correctly describe
the combustion evolution during the early ignition stage.
Electric Circuit
The energy that is required to
successfully initiate combustion—which is initially stored as electrical energy in
the ignition system—is converted to thermal energy when it is released into the
spark gap. The evolution of the electrical energy
in the secondary circuit is given as:
where
is the inter-electrode voltage,
is the current, and
is the resistance.
Not all of the electrical energy is
transferred to the spark—a substantial amount is lost by the Joule effect. The
intensity in the secondary circuit is estimated by:
where
is the circuit inductance.
At breakdown, the spark length is
equal to the spark gap
. The spark is then stretched by convection
and by the turbulent motion
. The total length of the spark is given
by:
The spark wrinkling evolution equation of
takes the form:
where
and
are the spark strains—that are caused by the
turbulent flow, and the mean flow, respectively.
corresponds to the effect of the turbulent eddies
that are greater than the arc thickness, but less than half of the length of the
spark. The computation of
is similar to the ITNFS function (net flame stretch
function) in the equation for the flame surface density.
During the arc and glow phases, only a
fraction of the spark energy is released to the gas. The energy that is released in
a thin region near the electrodes is essentially lost due to a fall in the voltage.
The voltage distribution during the arc and glow phases is represented by the
following diagram:
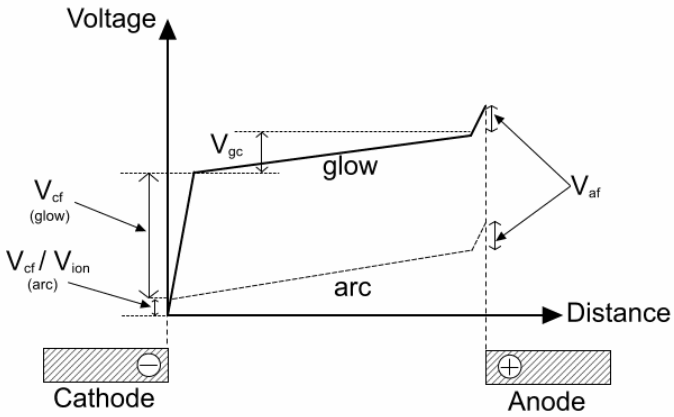
The electric potential difference
between the electrodes (the spark voltage) is given by:
where
,
,
and
are the cathode voltage drop, anode voltage drop,
the ionic potential of the cathode, and the gas column voltage, respectively. The
anode voltage drop is similar for both the arc and glow modes.
For Inconel (an alloy based on nickel,
chrome, and iron),
is 7.6V. During the arc phase,
is included in
, and is equal to 252 V during the glow phase.
The gas column voltage is given
by:
The breakdown and arc phases are
complex due to the extremely short duration, presence of a plasma channel, very high
temperatures, and unsteady behaviour. At breakdown, about 60% of breakdown energy
(which is a function of the spark gap
and the breakdown voltage
) is released to the gas, and provides the ignition
energy
that is required for the glow phase. The breakdown
energy is expressed as:
where
and
are constants.
The breakdown voltage
is expressed as:
where
is the density at standard conditions,
is a user adjustment parameter for the first
breakdown voltage evaluation,
, and
is a correction function—which is dependant on the
thermodynamic conditions and is different for the first breakdown and secondary
breakdown (restrike).
- First Breakdown
-
- Secondary Breakdown
-
- No Correction
-
- Corr. Factor
-
- Corr. Factor, Rho_g and EGR Mod
-
- Corr. Factor, Rho_plasma Mod
-
is a user adjustment parameter for the second
(restrike) breakdown voltage evaluation,
is the EGR mass fraction near the spark, and
is the plasma density which is determined
by:
where
is the increase in temperature due to the spark
energy.
During the glow phase, the voltage
drop is localised in the vicinity of the electrodes. It is therefore assumed that
the energy that is released within this region is lost to the electrodes. Finally,
the energy that is transferred to the gas is deduced from the gas column voltage and
current by:
ISSIM also accounts for the turbulent
dilution of the energy release by the spark outside its influence zone with the
following equation:
where
is a user constant, and
is a spark turbulent mixing timescale.
contributes to locally increasing the gas
temperature around the spark, and is distributed on the volume mesh according to a
Gaussian pdf, which adapts itself in one of two ways:
- height
-
has a fixed value of 2.
- width
-
varies to respect an acceptable increase
of temperature.
where
denotes the cell centroid and
is the spark location coordinates.
is used to decide if ignition has occurred or not.
It is also assumed that a flame kernel forms around the spark, and ignition starts
only if
within a minimum ignitable volume fraction around
the spark
.
is a critical ignition energy that depends on
thermodynamic properties in the vicinity of the spark:
where
can be defined as
or
.
is the flame thickness,
is the absolute pressure, and
is the ratio of the specific heats.
Under these conditions, an amount of
burnt gas
is produced at the spark, equivalent to the mass in
a cylinder of radius
and height
. There are three options available to evaluate
:
- Minimum Critical Burning Mass
-
- From Actual Spark Energy Released
-
- From Fixed Plasma Temperature
-
where:
-
is a user specified initial ignition burnt
mass coefficient
-
is the density of the unburnt gas
-
is an assumed temperature of plasma of 10000
K
-
is the specific heat of the burnt gases at
constant pressure
-
means average over a sphere that is centered
on the spark plug location and weighted by a Gaussian type probability
density function (PDF) in the radial direction of the sphere
Flame Kernel Growth Using ISSIM
If the critical energy criterion is
satisfied, an initial burnt gas mass is produced. This is evaluated using a target
burnt gas volume fraction
defined by:
where
is the spark gap,
the distance away from the spark plug location
, and the constants
and
satisfy the conditions:
and
or
In order to assign a value of
in the 3D computational domain, the reaction rate of
the progress variable
is written as:
where
is the laminar flame speed,
the flame surface density,
and
are the density of the burnt and unburnt gas,
respectively. In the above expression, the flame surface density (FSD) of a possible
pre-existing flame is also taken into account. This allows the consideration of the
interaction between flames coming from different spark ignitions.
The main purpose of ISSIM is to model
the reaction rate of a growing flame kernel via the FSD equation starting from the
very beginning of spark ignition. As a result, the equation needs to be initialised
as soon as the initial burnt gas kernel of radius
is created. The following expression is proposed for
this purpose:
The term
is chosen in order to recover the initial total
flame surface of a sphere of radius
so that:
It is also possible to provide
ignition source terms after the initial burnt mass deposit from the resolution of
the OD equation of the flame kernel radius, instead of using the source terms from
the flame surface density equation. In this case, flame surface density (if
available) is only initialized after transition from ignition to combustion if the
flame surface density equation is solved. This option is mostly used with the
complex chemistry model which does not evaluate flame surface density.
OD Flame Kernel Radius Equation
It is possible to solve the flame
kernel radius from a 0D equation:
where
and
are the unburnt density and burnt density
respectively, and
is a dynamic turbulent flame speed given
by:
where
is a modified effective laminar flame speed that is
due to the influence of energy that is released by a spark and the curvature of the
flame kernel.
is a dynamic turbulent wrinkling factor that is
given by:
where
and
denote the kernel radius surface at time step
and
respectively.
is the turbulent wrinkling production source, given
by:
where
is an adjustment constant, and
is a function of
,
,
,
, and
, which denote the turbulent fluctuation velocity,
turbulent integral length scale, Kolmogorov turbulent length scale, kernel radius,
and laminar flame thickness, respectively.
The fully turbulent wrinkling factor
is given by:
where
is an adjustment constant and
is a correlation function of
.
is the effective laminar flame speed.
Combustion heat release and associated reactions are fully driven by this flame
kernel radius equation in the influence zone of the spark up to the transition to
fully turbulent combustion that is driven by the combustion model itself.
Transition happens when the flame
kernel radius
is bigger that the kernel radius transition
, which is given by:
where
is a maximum transition radius constant,
is the initial kernel radius given by the initial
burnt mass deposit,
is a transition ratio constant, and
is the turbulent length scale.
The evolution of this kernel radius
allows the combustion progress variable to be updated on the 3D mesh from the same
distribution function that is used in
Eqn. (3985), and burnt mass conservation,
providing the species source terms with:
where
is the existing combustion progress variable, and
is the updated combustion progress variable from
ignition.
Modification of the FSD equation: Source terms at the spark plug in the presence
of a spark
As long as the spark exists
(
), the ignition criterion defined by
is calculated at the spark plug. Once this criterion
is satisfied, we assume that a burnt gas kernel corresponding to the ignition burnt
gas mass
exists at the spark plug. Without convection, the
burnt gas mass is only produced at the spark timing interval and this condition is
always satisfied. If the flame is convected away from the spark, it is replaced by
incoming fresh gases which ignites in the vicinity of the spark. If the ignition
criterion is satisfied, a target profile
is imposed at any instant. In the RANS approach, the
profile of
diffuses rapidly so that
. As a result, the burnt gas mass that is produced in
the vicinity of the spark is overestimated. The following diagram shows a
one-dimensional illustration of the progress variable evolution at spark time:
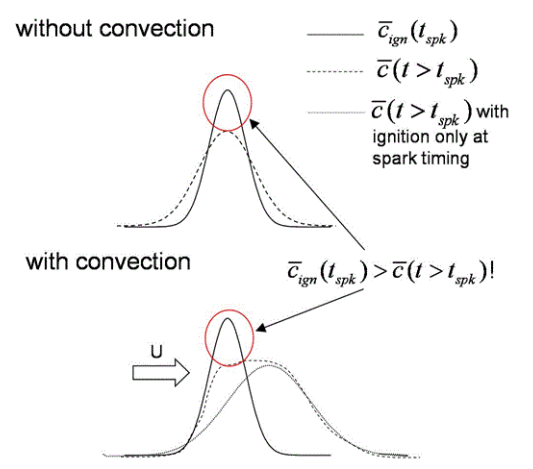
A solution to this problem is to
determine the right amount of burnt gas mass
that is produced around the spark. This amount,
which should be non-zero after spark ignition only if the flame kernel is convected,
can be estimated using a phenomenological approach as illustrated in the diagram
below which shows the burnt gas mass that is produced at the spark upon flame kernel
convection:
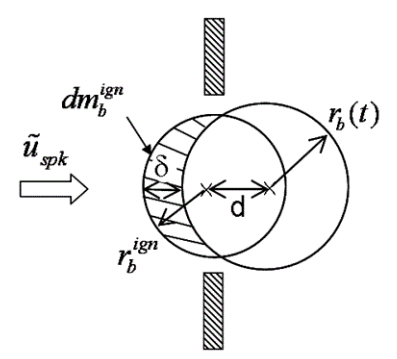
The mass
corresponds approximately to the mass of a
parallelepiped of height equal to the spark gap (
), depth
, and width
and is given by:
where
is the result of the evolution of the flame kernel
radius as a function of time. As the spark life is very short, we neglect the flame
wrinkling and the pressure variation effect. Several tests have shown that these
assumptions are reasonable. As for the initial burnt gas mass, the target burnt gas
volume fraction
is defined by requiring that the constant
satisfies the condition:
The spark source term
in
Eqn. (3909) for the ECFM model is expressed
as:
A consequence of this modelling choice is that if ignition is successful at breakdown
time and thereafter, the flame holder effect can be retrieved.