Directed Meshing Properties
This topic describes the Properties of each of the nodes that are available for directed meshing.
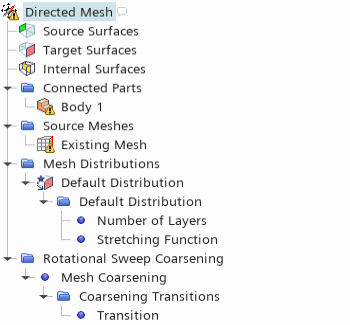
Directed Mesh Properties
- Input Parts
- Allows you to select one or more suitable parts from which to create a directed mesh. See Preparing CAD Parts For Directed Meshing and Preparing No-CAD Parts for Directed Meshing.
- Mesher Execution Mode
- Allows you to set the execution mode when running parallel servers. You can choose to run the mesh in two modes:
- Serial – part collections are queued for meshing on the main processor only.
- Concurrent –part collections are queued for meshing on multiple processes (see Concurrent Meshing).
- Generate Internal Surfaces (1-1 Direct Meshing only)
- Provides the option of creating internal surfaces within the directed mesh. There are two options for this:
- Activated—creates a node which allows you to define an internal mesh faces between the channels of a directed mesh.
- Deactivated—no internal faces are created within the directed mesh.
- Rotational Sweep Coarsening
- When activated, adds a node by which you control the rotational sweep coarsening feature that adds successive layer transitions across which two or more cells are merged into a single cell.
Source Surfaces Properties
- Source Surfaces
- Allows you to select one or more surfaces to represent the source surface.
Target Surfaces Properties
- Target Surfaces
- Allows you to select one or more surfaces to represent the target surface.
Internal Surfaces Properties
- Internal Surfaces (1-1 Direct Meshing only)
- Allows you to select a previously created empty part surface on which to create internal mesh faces. Mesh faces run along the internal and external sides of a channel running from a source mesh face, through the volume mesh, to the corresponding target mesh face.
If the part surface is assigned to a wall boundary, cross flow is not allowed between the channels. This functionality is useful when performing CFD analyses of heat exchangers which model hot and cold fluid streams through channels in a porous region between periodic interfaces.
Connected Parts – Part Properties
Each [part] node is named after the connected geometry parts that are selected for directed meshing.
- Parts
- Displays the names of the connected geometry parts that are selected for directed meshing.
- Source Mesh Node
- Displays the source mesh that is associated with the connected part.
- Target Surface Mesh Smoothing
- Controls whether the target surface mesh is smoothed. Activate this option to use the smoothing algorithms within the mesher. In some cases, such as simple cube and cylinder shapes, it is not necessary to smooth the target surface mesh. In other cases, smoothing a target surface mesh can deteriorate the surface mesh quality (this is especially true of M-1 direct meshing of more complex parts. In such cases, deactivate the smoothing of the target surface mesh.
Source Meshes – Existing Mesh Properties
Each source mesh node is named after the contacting part collection which the source mesh is defined on.
- Source Mesh From
- Specifies the source mesh. Choose from:
- Contacting Volume Mesh – Extracts the mesh from a volume mesh that contacts the specified source surfaces.
- Triangle Mesh – Extracts the latest triangle mesh of the part or parts being meshed. If the original triangulation is obtained, the source mesh that is extracted can be of poor quality if it contains long, narrow triangles. If the part is remeshed, the remeshed triangulation is obtained.
- Quadrilateral Mesh – Obtained from the extracted triangulation. The mesh is dependent upon the quality of the extracted triangulation. The quadrilateral mesh that is obtained is quad-dominant with a mix of quads and triangles. The quadrilateral mesh does not faithfully replicate the extracted triangle mesh density.
- Part Surfaces
- Displays the part surfaces that are specified as the source surface meshes on the connected part.
Mesh Distributions
- [Distribution] Properties
- Part Collections
- Sets the part collection to which this distribution is applied.
- Mesh Controls
- Allows you to create custom controls for each connected part in the directed mesh operation.
- Use Default —allows you to specify the number and size of layers for all connected parts together.
- Specify Custom—exposes the node which allows you to create part controls for customizing the number of layers and stretching function for each connected part.
- Size Specification
Sets the method by which the mesher determines the size of successive cell layers throughout the distribution. This choice affects the value nodes that you see under Default or Custom Controls.
- Number of Repetitions
- Sets the number of times the volume mesh distribution is repeated between the source and the target surface. This repetition can be useful when meshing stacks of parts.
- Stretching Function Properties
Stretching Method Value Nodes - Constant
- No stretching applied.
None - One Sided Geometric
- Applies geometric progression to compute cell thickness.
- One Sided Options
- Set the Stretching Mode to one of the following options and then set the required value in the child node:
- Stretching—ratio of spacing at layer n and layer n+1
- Initial Wall Thickness—spacing at the first layer of cells
- Thickness Ratio—ratio of spacing between first layer and last layer of cells
- One Sided Hyperbolic
- Hyperbolic-based stretching to compute cell distribution.
See One Sided Options above. - Two Sided Hyperbolic
- Hyperbolic stretching from both ends to compute cell distribution.
- Two Sided
- Sets the following properties:
- Spacing at Source—initial spacing at the source surface
- Spacing at Target—initial spacing at the target surface
- Reverse Direction—activate in order to swap direction
Mesh Distributions – Custom Controls
When the Mesh Controls property for a Volume Distribution is set to Specify Custom, a Custom Controls node appears in which you can set specific property values for chosen parts.
- Part Control Properties
- Parts
- Parts for which the custom control applies.
- Enable Control
- Activates the functionality of the Part Control.
- Controls Display Mode
- Choose to show All controls or only those you have already Customized.
- [part control] Properties
- Depending on your choice of Size Specification, you either see controls appropriate when setting the number of layers or those appropriate for size-based distributions. By default each control is set to Use Auto Computed Value. To define a custom value, set the option to Specify Custom Value, and then set the appropriate quantities beneath the Value node.
- Custom Controls Node Right-Click Action
- New Part Control
- Creates a Part Control sub-node which allows you to customize the Properties of a part or parts that you select.
Rotational Sweep Coarsening – Mesh Coarsening Properties
The following Properties are available to set when you select the node.
- Part Collections
- Sets the part collection to which this rotational sweep coarsening is applied.
- Transition Controls
- Defines the how the mesh transitions between the core mesh and the coarse mesh. There are two options for this:
- Use Default—automatically computes where transitions are required in order to meet the constraints of the Aspect Ratio.
- Specify Custom—Adds a node which allows you to create one or more transitions manually.
- Aspect Ratio
- For a given mesh face on the guide surface the Aspect Ratio is the ratio of edge length in the radial direction to the edge length in the azimuthal direction. Coarsening tries to merge cells/faces such that the aspect ratio in the final mesh does not exceed the specified value. Transitions are computed automatically and the merge ratio at each transition is set to 2 by default. Specifying a smaller aspect ratio results in coarsening spreading further away from the rotational axis. The aspect ratio in the default setting is mainly intended to be used with constant stretching function in volume distribution.
- Coarsening Transition Properties
- Distance from rotational axis
- The radial distance from the rotational axis at which this coarsening transition applies.
- Merge ratio 1:
- The number of cells that match a single cell, in the radial direction, across a transition.
- Enable control
- When activated, allows you to specify the properties of the transition in the window, and applies the transition when you generate the volume mesh.