Contact with a Rigid Surface
A rigid contact constraint defines a boundary condition on the surface of a deformable solid. This boundary condition accounts for the contact between the solid and a rigid surface that is not part of the stress analysis.
Currently, Simcenter STAR-CCM+ allows you to model frictionless contacts with rigid planes.
Contact Pressure
Consider the interface
The traction
vector on
where
For frictionless contacts, the only contribution to the traction vector comes from the normal component, that is, the contact pressure. The contact pressure on the initial surface is related to the pressure on the current, deformed, surface through:
where
The contact conditions in
the normal direction can be formulated as a Karush-Kuhn-Tucker
condition [870]. For each point on the
contact surface
where
Contribution of the Contact Pressure to the Virtual Work
For frictionless contacts, only the contact pressure contributes to the virtual work equation for the deformable solid (Eqn. (4464)), which becomes:
where the last term on the
left-hand side is the contact contribution. The variation of the
contact gap
where
Penalty Method for Contact Enforcement
Simcenter STAR-CCM+ models the relationship between the contact pressure and the gap function using the penalty method. The penalty method models the hard contact by penalizing any nonphysical penetrations of the solid body into the rigid surface.
With this approach, the
where
and
The penalty method
describes a perfectly rigid contact only for
where
Uzawa Algorithm for Contact Enforcement
where
where
Discretization of the Rigid Contact Gap
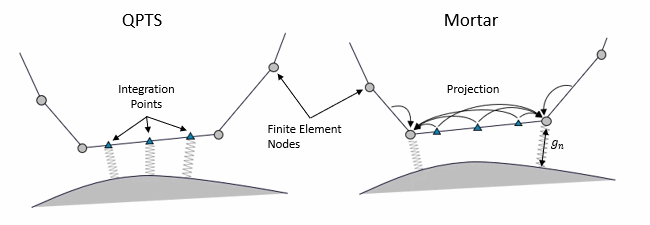
- Quadrature Point to Surface scheme (QPTS)
- The quadrature point to surface scheme (QPTS) computes
the exact contact gap for the finite element
integration points using Gaussian integration, and
applies the penalty method directly to the contact
gap values for the integration
points:(4498)
- Mortar
- In contrast, the Mortar discretization introduces a
finite element discretization of the contact
pressure:(4499)