Defining Contact with a Rigid Obstacle
Simcenter STAR-CCM+ allows you to model contact between a deformable solid and a rigid obstacle using a rigid contact constraint. With this approach, you model the effect of the contact on the deformable solid, without modeling the obstacle explicitly.
The contact formulation is based on a surface-to-surface approach, which considers the contact gap at the quadrature points used in the numerical integration of the contact virtual terms (see Contribution of the Contact Pressure to the Virtual work). The post-processing displays results evaluated on either the vertices or face centroids, depending on whether the contour style is set to smooth or filled, respectively. Hence, the post-processed contact gap may not converge to zero at the vertices or face centroids. You are advised to use a finer mesh to improve the post-processsing results.
To create a rigid contact constraint:
-
Create a surface segment with the following properties:
Node Property Setting [Segment] Surfaces Select the surface of the deformable solid that comes into contact with the rigid obstacle. Type Constraint Method Rigid Contact -
To define the rigid contact surface, select one of the following options:
- To define a rigid plane:
- Select the Plane. node and set Contact Obstacle to
- Select the
Property Setting Origin Define the coordinates of the origin. Normal Define the surface normal vector. The plane surface normal must point outwards with respect to the plane surface, that is, it must be opposite to the solid surface normal at the point of contact. Coordinate System Specify the coordinate system in which the origin and surface normal are defined.
node and set the following properties:
- To define a rigid cylinder:
- Select the Cylinder. node and set Contact Obstacle to
- Select the
Property Setting Cylinder is Specify the body type of the cylinder. There are two options for this: - Filled - cylinder is defined as a solid body.
- Hollow - cylinder is defined as a hollow shell and allows you to model a pipe.
Cross Section Define the cross-sectional shape of the cylinder. There are two options for this: - Circle - the cross section of the cylinder is defined as a circle.
- Ellipse - the cross section of the cylinder is defined as a ellipse.
Radius (for Circle Cross Section only) Define the radius of the circle Radius-x (for Ellipse Cross Sections only) Define the radius of the ellipse in the X direction Radius-y (for Ellipse Cross Sections only Define the radius of the ellipse in the Y direction Coordinate System Specify the coordinate system used to define the cross section and extrusion direction of the cylinder. The cross section is defined in the X-Y plane of the specified coordinate system, while the extrusion direction is defined by the Z axis.
node and set the following properties:
- To define the surface of the rigid obstacle using geometry
parts:
- Make sure that the geometry parts that define the rigid
obstacle satisfy the following requirements:
- The tessellated surfaces of the geometry parts are closed.
- The geometry parts are not from an imported CAE model.
- The geometry parts are not assigned to the solid region.
- If the geometry part is a shell part, the front surface of the part faces the solid region.
- Select the Tessellated Geometry Parts. node and set Contact Obstacle to
- Select the node and set Tessellated Geometry Parts to the parts whose tessellated surfaces define the rigid obstacle.
- Make sure that the geometry parts that define the rigid
obstacle satisfy the following requirements:
- To define a rigid plane:
To define the Rigid Motion of the Tessellated Geometry Parts:
- Right-click New and define the rigid motion as required. For more information on the available motions and their properties, see 模拟刚体运动 and 刚体运动模型参考. , select
- Select the node and set Rigid Motion to the rigid motion that you defined.
- Right-click the node and select .
- Set Motion to the rigid motion.
- In a Scene, create a Geometry Displayer for the parts that form the moving obstacle and set the following properties:
Property | Setting |
---|---|
Representation | Latest Surface |
Transform | [Motion Transform] |
To post-process the time history of the motion once the simulation has finished:
- Set the Recorded Representation of the [Motion Transform] to Solution View stored in the .simh file. See, Retrieving Transient Solution Data.
-
As the projection is defined in the Latest Surface
description, check that the Latest Surface description
of the Tessellated Geometry Parts is as expected.
You can modify the Latest Surface in many ways. For example, through Operations, Surface Repair, or the Re-Tessellation of parts.
You can manually increase or decrease the geometric contact gap by specifying a Contact Gap Offset (see Contact Gap Offset). Specifying an offset is particularly useful when the rigid obstacle is a tessellated part, as the location of a tessellated part is generally more difficult to manipulate than the location of a rigid plane or cylinder.
To change the geometric contact gap between the rigid obstacle and the surface of the deformable body:
-
Select the
node and set Contact Gap Offset to the
value you want to increase or decrease the geometric contact gap by. Positive values increase the contact gap, whereas negative values decrease it. For example, if you want to model the contact between a solid surface and a tessellated part surface as being closed, yet the surfaces are in fact separated due to tolerances in the CAD model or mesh, you can close the contact gap by setting the Contact Gap Offset to the tolerance size.
-
To visualize the contact gap, use the Contact Gap field
function in a plot or scene.
You can visualize the contact gap on parts, regions, boundaries, segments, and derived parts, as well as record the field function to a .simh file.
- Quadrature Point to Surface (QPTS), which computes the contact gap at the integration points and directly applies the penalty method to compute the contact virtual work (see QPTS)
- Mortar, which considers a finite element discretization of the contact pressure. The contact gap is projected onto the same discretization before applying the penalty method (see Mortar).
To select the discretization method:
-
Select the
node and set the appropriate Method.To use the Augmented Lagrangian (Uzawa algorithm) contact enforcement method (see Contact Constraint Enforcement) select the Mortar discretization. To reduce the constraints on the contact, you are recommended to use the Mortar discretization method.
In both methods, you specify the penalty parameter that defines the allowed nonphysical penetration:
-
Select the
node and set the Penalty Parameter
value.In general, the larger the penalty parameter, the smaller the nonphysical penetrations. However, very large values can cause convergence issues, whereas small values can lead to nonphysical contact modeling. Ideally, the parameter should be as large as possible, within the convergence limit.
-
Expand the
node and set the following properties:
Node Property Setting Contact Discretization Method Mortar Contact Constraint Enforcement Enforcement Method Augmented Lagrangian (Uzawa algorithm)
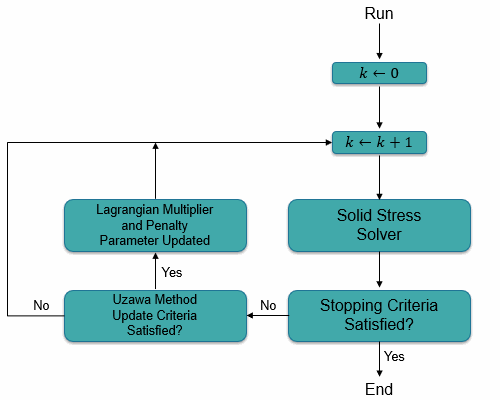
To trigger this additional loop, specify the Uzawa controls:
-
Expand the
node and define the following nodes:
- Maximum Steps per Uzawa Update
- Uzawa Update Displacement Criterion
- Uzawa Update Force Criterion
The Uzawa Update Displacement Criterion and Uzawa Update Force Criterion compare the current force and displacement residual value to the tolerance you have specified. If the residual values are lower than the tolerance specified the Uzawa update loop is triggered. The Maximum Steps per Uzawa Update control limits the maximum number of iterations for the Solid Stress solver per Uzawa augmentation.
-
Select the Contact Constraint Criterion nodes,
and define the required properties.
, or To provide the best convergence for the case, you are recommended to activate the Force Criterion or Displacement Criterion along with the Contact Pressure Criterion. Use a Minimum Limit for the contact pressure and set the Logical Rule to AND for both the Solid Stress stopping criteria (Force Criterion and Displacement Criterion) and the Uzawa algorithm stopping criteria (Contact Pressure Criterion and Contact Constraint Criterion).
The Contact Pressure Criterion compares the difference between the current contact pressure and the Lagrange multipliers, whilst the Contact Constraint Criterion evaluates whether the contact conditions have been violated. For more information, see Uzawa Algorithm for Contact Enforcement.
-
Select the
node and activate Penalty Parameter
Update.When this property is activated, you can also define the maximum value of the penalty parameter using the Penalty Parameter Upper Bound property.
-
Select the Complete.
node and set Linearization of Contact
to This setting improves convergence when the rigid obstacle is a curved surface. Curved surfaces do not include tessellated surfaces, which are comprised of flat triangles that do not capture the surface curvature. Contact Linearization can affect the stability of the simulation. For more information, see Contact Linearization.