The
Solid Stress model allows you to compute the displacement of solid structures under loads, using the finite element approach. This model is the prerequisite for all types of stress analysis.
Theory
|
See
固体力学.
|
Provided By
|
|
Example Node Path
|
|
Requires
|
Physics Models:
- Space:
Three Dimensional
- Material:
Solid or
Multi-Part Solid
|
Compatible Meshers
|
- Directed Mesher
- Tetrahedral Mesher
- Thin Mesher
|
Activates |
Physics Models
|
Material Law Models. See
Material Law Models Reference.
|
Material Properties
|
For each solid material,
Simcenter STAR-CCM+ activates mechanical and thermal properties based on the specified material law. See
Material Law Models Reference.
|
Reference Values
|
Geometry Refinement Specification
|
Initial Conditions
|
See
Initial Conditions.
|
Boundary Types
|
Wall,
Symmetry Plane. See
Boundary Types.
|
Region Inputs
|
- Body Load
Derivative
- Body Load
Option
- Mid-side
Vertex Option
See Region Settings. |
Region Nodes |
Segments. See
Segments (Loads and Constraints) Reference. |
Interface Inputs
|
- Mechanical Interaction (for solid/solid interfaces of type
Mapped Contact Interface).
- Constraint Mapping (for bonded solid/solid interfaces of type
Mapped Contact Interface).
See
Interface Settings.
|
Solvers
|
- Solid Stress Solver
- Sparse Direct Solver
See
Solid Stress Solver Reference and
FE 稀疏直接求解器参考.
|
Monitors
|
- Displacement
- Force
- Strain Energy
See
Monitors.
|
Field Functions
|
Applied
Force, Body Force, Constraint Force,
Contact
Gap, Contact Pressure, Discrete Contact Gap,
Displacement, Element Type,
Internal
Force, Log Strain Tensor,
Rigid Body
Acceleration, Rigid Body Force,
Rigid Body
Velocity, Strain Tensor, Stress Max. Shear,
Stress
Mean, Stress Tensor, Stress Von Mises
See Field Functions.
|
Reports
|
See
Reports.
|
Stopping Criteria |
- Displacement
Criterion
- Force Criterion
- Contact Pressure Criterion
(activated when Contact Constraint
Enforcement is set to Augmented Lagrangian (Uzawa algorithm))
- Contact Constraint Criterion
(activated when Contact Constraint
Enforcement is set to Augmented Lagrangian (Uzawa algorithm))
- Number of Uzawa Updates (activated
when Contact Constraint Enforcement
is set to Augmented Lagrangian (Uzawa
algorithm))
- Strain energy Criterion (activated when
Strain energy is activated)
See Stopping Criteria. |
Reference Values
- Geometry Refinement Specification
- When you constrain a surface,
Simcenter STAR-CCM+ applies the constraint on the mesh vertices that lie on that surface (see
Solid Stress Constraints). For accurate boundary conditions, it is important that the geometry of the surface is locally captured.
- To represent the geometry of curved surfaces,
Simcenter STAR-CCM+ evaluates unique vertex normals at each mesh vertex by averaging the normals of the adjacent mesh faces
[131]. The vertex normals provide a more accurate representation for radial (normal) directions.
- On a feature edge, where two different surfaces meet,
Simcenter STAR-CCM+ must retain multiple normals per vertex.
Simcenter STAR-CCM+ recognizes a feature edge between two surfaces based on the specified
Dihedral Angle Tolerance. If the angle between the adjacent face normals exceeds the specified tolerance,
Simcenter STAR-CCM+ retains multiple normals. If the angle between the adjacent face normals is within the specified tolerance,
Simcenter STAR-CCM+ generates a unique vertex normal.
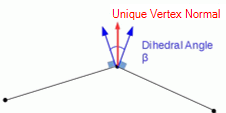
- In general, you are advised to leave the
Dihedral Angle Tolerance as the default value.
- For surfaces meeting at small angles, you can decrease the
Dihedral Angle Tolerance so that
Simcenter STAR-CCM+ recognizes the feature edge shared by the two surfaces. For coarse meshes, where different faces of the same surface meet at large angles, you can increase the
Dihedral Angle Tolerance so that
Simcenter STAR-CCM+ recognizes the surface as continuous and generates the unique vertex normal.
- You can specify the
Dihedral Angle Tolerance independently in each region using the
Geometry Refinement Option. See
Region Inputs.
-
注 | For vertices that lie on symmetry plane boundaries, the calculation of vertex normals is consistent with the full geometry resulting from the symmetry condition.
|
Initial Conditions
- Displacement
- Allows you to specify the initial displacement as a vector profile.
Stress analysis requires you to constrain the solid structure by prescribing the displacement vector at appropriate surfaces, curves, or points (see
Applying Constraints). In dynamic analyses, the specified constraints take precedence over the initial conditions when conflicts occur. During the first iteration, the displacement solution transitions from the initial condition to the specified constraint. After the first iteration, the solid structure deforms under the specified loads and constraints. Specifying a nonzero initial displacement for the unconstrained degrees of freedom can lead to unbalanced residual forces and divergence of the solution.
- Velocity
- Allows you to specify the initial velocity as a vector profile.
Boundary Types
- Wall
- By default, wall boundaries are free from loads and constraints. Wall boundaries present a
Stress/Displacement physics condition, which is always set to
Free. This condition is read only, as you define loads and constraints on the associated part surfaces using segments. See
Segments (Loads and Constraints) Reference.
- Symmetry Plane
- At symmetry plane boundaries,
Simcenter STAR-CCM+ automatically sets the normal component of displacement to zero. As with wall boundaries, you can define loads and constraints on the associated part surfaces using segments (see
Segments (Loads and Constraints) Reference.). However, do not define constraints that specify a nonzero normal displacement, as this would result in conflicting constraints.
Region Settings
Applies to solid regions.
- Body Load Derivative
- Only available when you set Body
Load Option to Specified.
- Allows you to define the partial derivatives
of the body force with respect to displacement, velocity, or acceleration.
You can define more than one derivative in the same simulation.
Properties |
Corresponding Physics Value Nodes |
- Displacement
Derivative
- Allows you to specify the displacement derivative
(
in Eqn. (4571)).
|
- Body Load Displacement
Derivative
- Specifies the derivative as a Composite Symmetric Tensor, Composite Tensor, Isotropic Tensor, or
Principal
Tensor.
|
- Velocity
Derivative
- Allows you to specify the velocity derivative
(
in Eqn. (4572)).
- Only
available for unsteady simulations.
|
- Body Load Velocity
Derivative
- Specifies the derivative as a Composite Symmetric Tensor, Composite Tensor, Isotropic Tensor, or
Principal
Tensor.
|
- Acceleration
derivative
- Allows you to specify the acceleration derivative
(
in Eqn. (4573)).
- Only
available for unsteady simulations.
|
- Body Load Acceleration
Derivative
- Specifies the derivative as a Composite Symmetric Tensor, Composite Tensor, Isotropic Tensor, or
Principal
Tensor.
|
- For each body load derivative you can also
define the Coordinate System the tensor is defined
in under the node. If you are using a local coordinate system, it is
recommended you use the same coordinate system for both the Body Load Derivative and Body Load Option. In this case, you can also express the body
load in terms of the displacement field function with respect to the local
coordinate system (see Referencing Local Coordinate
Systems).
- Body Load Option
- Allows you to apply a body force on the region. Its counterpart in CFD is the Momentum Source Option. The Body Load Option is intended for body loads which are independent of the stress and strain, but may be a function of the displacement field.
-
Method |
Corresponding Physics Value Nodes |
- None
- No body forces are applied.
|
None |
- Specified
- Allows you to apply a body
force on the region. For the body force, you can
also specify its derivatives with respect to
displacement, velocity, and acceleration.
|
- Body Load
- Defines the body force
vector
in Eqn. (4570) along with the
Coordinate System the
vector is defined in.
- Body Load
Derivatives
- Allows you to define the partial
derivatives of the body force with respect to
displacement, velocity, or acceleration (see Body Load Derivatives).
|
- Geometry Refinement Option
- For a given region, allows you to overwrite the Dihedral Angle Tolerance specified in the physics continuum (see
Geometry Refinement Specification).
-
Option |
Corresponding Physics Value Nodes |
- Use Continuum Values
- Sets the
Dihedral Angle Tolerance to the value specified in the associated physics continuum. See
Geometry Refinement Specification
|
None |
- Specified
- Sets the
Dihedral Angle Tolerance to a specified value.
|
- Geometry Refinement Specification
- Specifies the
Dihedral Angle Tolerance for the region. This value overwrites the physics continuum
Geometry Refinement Specification.
|
- Mid-side Vertex Option
- Allows you to add or remove mid-side vertices. By default,
Simcenter STAR-CCM+ mesh operations generate linear elements without mid-side vertices.
- Although you can change this setting at any time during a simulation,
Simcenter STAR-CCM+ adds or removes the vertices during initialization, when you run the simulation. To verify the mesh element topology, you can visualize the Element Type field function in a scalar scene for the part. For more information, see
Mesh Requirements and Guidelines.
- The available methods are:
- Add -- Linear Interpolation—adds mid-side vertices (nodes) as linear interpolates of the vertices on either end of an edge. This option adds mid-side nodes to each edge of every element of the mesh. When you add mid-side nodes,
Simcenter STAR-CCM+ also interpolates any previous solution, computed on the linear mesh, to the mid-side vertices. The addition of mid-side nodes forces a new evaluation and factorization of the stiffness matrix.
- Keep Original—keeps the original mesh element configuration. If you generated the mesh in
Simcenter STAR-CCM+, and you have not added mid-side nodes, the mesh elements remain linear. If you have added mid-side nodes, the mesh elements remain quadratic. If you imported the mesh through an imported CAE model, the element topology remains linear/quadratic, based on the original configuration.
- Remove All—removes any mid-side nodes. This option includes mid-side nodes that were added in
Simcenter STAR-CCM+, or mid-side nodes that were imported with a CAE model. The removal of mid-side nodes forces a new evaluation and factorization of the stiffness matrix.
Region Controls
- Segments
- Activating the Solid
Stress physics model automatically creates a
Segments folder in the regions node. If you
deactivate the Solid Stress model, and no segments
are present, Simcenter STAR-CCM+ also
removes the Segments folder. See Segments (Loads and Constraints) Reference.
Interface Settings
Interfaces can be conformal or
non-conformal, but not imprinted. Imprinting may create polyhedral cells, which are
not supported in finite element analysis. The available conditions are:
- Mechanical Interaction
- Available for solid/solid interfaces of type Mapped Contact
Interface.
- Specifies the type of interaction between the contacting surfaces. This condition is available for mapped contact interfaces with
Topology other than
Periodic. The available options are:
-
- Bonded—the contacting surfaces undergo continuous displacements. If the solid regions are different materials, discontinuities in the strain are preserved across the material interface. Activates the
Constraint Mapping condition.
Simcenter STAR-CCM+ automatically treats periodic interfaces, contact interfaces, and internal interfaces as
Bonded.
- Small Sliding
Frictionless—allows the contacting
surfaces to slide over each other in the direction tangential to the
interface, whereas movement in the normal direction is prohibited.
The shear stress at the interface is equal to zero, and the normal
forces are equal and opposite.
This option is
intended for small sliding at flat interfaces. Sliding of
vertices at curved interfaces, or sliding of vertices that
exceed the mesh element length, leads to inaccurate results.
This option
targets applications where unrealistic stress concentrations
would otherwise occur. For example, thermal-stress analysis
involving interfaces between materials with different thermal
expansion coefficients.
This type of
interaction is not compatible with the Solid
Displacement motion.
- 约束映射
- 可用于映射接触交界面类型的固体/固体交界面。
- 指定 Simcenter STAR-CCM+ 用于约束粘合表面的方法。可用选项如下:
- 节点至表面:
默认选项。在两个有限元之间的交界面处,次单元上的节点被约束到主单元上重叠表面的节点。通常,此方法所需的计算工作量较少,但它不保留线动量和角动量(在固体应力计算中)或热通量(在固体能量计算中),并且可能导致计算的应力或温度局部不精确。
- 表面至表面:
在两个有限元之间的交界面处,次单元与主单元的重叠表面将细分在三角形中。在重叠表面上广义积分或弱积分以满足约束。与
节点至表面方法相比,此方法保留线动量和角动量(在固体应力计算中)或热通量(在固体能量计算中),从而提高了计算的应力或温度的精度。但是,此方法需要更多的计算量,并且所需内存会随着使用的内核数而增加。
此选项仅适用于粘接映射接触交界面。滑动交界面自动使用节点至表面方法。
对于共享周长和节点的相邻交界面,建议使用相同的约束映射方法。使用这两种方法可能会导致过度约束共享节点。
Monitors
- Displacement
- Solid displacement increment [m] (see
Eqn. (4833)).
- Force
- Residual force [N] (see
Eqn. (4833)).
- Strain Energy
- Strain energy, defined with the unit of [Nm] (see
Eqn. (4838)). This monitor is available when you activate the
Strain energy property for the
Solid Stress Solver (see
Solid Stress Solver Reference).
With these monitors they have corresponding stopping criteria that automatically
becomes available when Solid Stress Solver is activated. See
Stopping Criteria.
Field Functions
- Contact
Gap
- Scalar field function that
represents the contact gap between the solid surface and rigid obstacle. The
contact gap is defined as the distance between a point on the solid surface
and the closest-point projection on the rigid obstacle surface. For the
contact gap calculation, Simcenter STAR-CCM+ considers a single closest point for all the surfaces
of the rigid obstacle. For very large penetrations, this closest point may
not correspond to the expected physical contact direction.
- The contact gap field
function reflects the geometric contact gap calculated by Simcenter STAR-CCM+ as well as any additional
Contact Gap Offset applied to the Rigid Contact
segment. For regions and contacting boundaries containing more than one
Rigid Contact segment, the region or face value is equal to the minimum
contact gap defined by the segments. For regions and boundaries which do not
belong to a Rigid Contact segment, the region or face value is equal to the
maximum contact gap available.
- This scalar field function is
available on:
- All Rigid Contact segments.
- Solid boundaries with at least one Rigid Contact segment
specified on the region. The part surfaces of the boundary do not
need to be assigned to a Rigid Contact
segment.
- Any solid region with at least one Rigid
Contact segment specified.
- Contact
Pressure
- For Mortar discretization of a rigid
contact, represents the Cauchy contact pressure (
in Eqn. (4482)) between the solid surface
and the rigid obstacle. Positive pressure corresponds to a compressive
load.
- The Contact pressure field
function is available on:
- All Rigid Contact segments.
- Solid boundaries with at least one Rigid Contact segment
specified on the region. The part surfaces of the boundary do not
need to be assigned to a Rigid Contact
segment.
- Any solid region with at least one Rigid Contact segment
specified.
- For regions, the contact pressure is equal
to the area-weighted contact pressure on the part surfaces that form the
Rigid Contact segments.
- Discrete Contact
Gap
- For Mortar discretization of a rigid
contact, represents the average contact gap from the projection of the
continuous contact gap to the finite element nodes (
in Eqn. (4500)).
- The discrete contact gap field function is
available on:
- All Rigid Contact segments.
- Solid boundaries with at least one Rigid
Contact segment specified on the region. The part
surfaces of the boundary do not need to be assigned to a
Rigid Contact segment.
- Any solid region with at least one Rigid
Contact segment specified.
- For regions, the discrete contact gap is
equal to the minimum discrete contact gap defined by the part surfaces that
form the Rigid Contact segments.
- Displacement
- Vector field function that represents the displacement in
Eqn. (4426).
- Element Type
- Scalar field function that identifies each element topology with a unique number. To visualize the mesh element type, display this field function in a scalar scene. If all the elements in the mesh are of the same type, the color bar will display a single number. The values associated with each element topology are listed in the section,
Element Type Reference.
- Log Strain
Tensor
- For non linear stress-strain
analysis, the tensor field function represents the spatial logarithmic
strain tensor, as defined in Eqn. (4449)
- Rigid Body
Acceleration
- Defines the
acceleration,
, in [eqnlink]. When you activate the
Coriolis - Solid Displacement Velocity Effect
model, the additional Coriolis acceleration term ([eqnlink]) is added to the rigid body acceleration.
- Rigid Body
Velocity
- Defines the
velocity of the body due to rotational and translational motions.
- Strain Tensor
- For linear
stress-strain analysis, the tensor field function represents the
infinitesimal strain tensor, as defined in Eqn. (4444). For non linear stress strain analysis, tensor field
function represent the Green-Lagrange Strain tensor, as defined in Eqn. (4445)
- Stress Max. Shear
- Scalar field function that represents the maximum shear stress, as defined in
Eqn. (4437).
- Stress Mean
- Scalar field function that represents the mean stress measure, as defined in
Eqn. (4438).
- Stress Tensor
- Tensor field function that represents the Cauchy stress tensor (see
Cauchy Stress).
- Stress Von Mises
- Scalar field function that represents the von Mises stress measure, as defined in
Eqn. (4440).
- Forces
-
- Applied
Force
- Vector field function that
represents the resultant of the applied surface and point loads.
At a node
, it is defined as:
- where
is a nodal shape function (see
Eqn. (4550)),
is the prescribed surface
traction integrated over the relevant surfaces
,
is the prescribed line load
integrated over the relevant curves
, and
is the point load prescribed at
node
.
-
- Body
Force
-
Vector field function that represents the resultant of the body
forces. At a node
, it is defined as:
-
- where
is the prescribed body load,
and
are the mass and damping
matrices (see Eqn. (4559) and Eqn. (4576)),
is the prescribed acceleration
and
is gravity.
- When the Coriolis - Solid
Displacement Velocity Effect model is activated,
the Coriolis acceleration ([eqnlink]) is included in the rigid
body acceleration
.
- Constraint
Force
- Vector field function that represents the reaction forces at
constrained boundaries and at interfaces.
- The
residual forces at a mesh node
,
can be expressed in terms of
free and constrained degrees of freedom,
. The residual forces of the free
degrees of freedom must approach zero at convergence,
. The negative residual forces of
the constrained degrees of freedom,
, are called constraint forces.
- Internal Force
- Vector field function that represents the internal elastic forces, as defined in
Eqn. (4558).
- Rigid Body
Force
- Defines the forces acting on
the body due to the rigid body motions.
The internal force, applied force, and body force at a mesh node are calculated as the sum of all element contributions connected to , that is, the integrals
Eqn. (344),
Eqn. (345), and
Eqn. (4558) are the sum over each element volume, surface, or edge associated with .
For more information on how to use these field functions in scenes and reports, see
Reports and
求解分析准则.
Reports
The Sum Force
and Sum Moment reports allow you to check for equilibrium of
all the forces and moments acting on specified input parts, as required by
conservation of linear and angular momentum. Each part and the sum of all input
parts must be in equilibrium. The Sum Force and
Sum Moment reports are defined with respect to a
Cartesian coordinate system.
- Sum Force
- Reports the
resultant of the applied, body, internal, or constraint forces on the
specified input parts. The input parts for this type of report can either be
geometry parts or regions.
- Simcenter STAR-CCM+ first calculates the force
resultants per input part, by summing all the forces at the part nodes, and
then sums the resultants calculated for each input part.
- For example, to
calculate the Sum Force of the Applied Force, Simcenter STAR-CCM+ calculates the resultant
of the Applied Force
for each input part, as:
-
- and then sums the
resultants calculated for each input part.
- Sum Moment
- Reports the
resultant moments of the applied, body, internal, and constraint forces,
acting on the selected input parts, with respect to a specified location
. Simcenter STAR-CCM+ first calculates the resultants of the moments per
input part, by summing all the moments at the part nodes, and then sums the
moment resultants calculated for each input part.
- For example, to
calculate the Sum Moment of the Applied Force, Simcenter STAR-CCM+ calculates the resultant
of the moment of the Applied
Force for each input part, as:
-
- and then sums
the resultants calculated for each input part.
Stopping Criteria
The Solid Stress Solver
has additional Stopping Criteria based on the convergence of
the displacement, force, contact constraint, contact pressure, and strain energy
residuals. For this solver, Simcenter STAR-CCM+
automatically adds the Displacement and Force stopping criteria. You can add the
Strain energy Criterion manually by activating the Strain energy property of the Solid Stress
Solver.
You can add the
Contact Constraint
Criterion,
Contact Pressure Criterion, and
Number of Uzawa Updates criteria by setting the
Contact Constraint Enforcement to
Augmented Lagrangian (Uzawa algorithm).
- Contact Pressure Criterion—monitors the
difference between the current contact pressure and the Lagrangian
multipliers (see Eqn. (4495))
- Contact Constraint Criterion—corresponds
to the current normalized contact penetrations (see Eqn. (4496))
- Number of Uzawa Updates—Limits the
number of times the Lagrangian multipliers are updated during the
simulation.
You can set the
Norm Type for these criteria under
the
Solid Stress Solver node and specify the normalization
option on the corresponding monitors. For the
Contact
Constraint monitor, the
Normalization
Option is
Off by default.
For more information on the properties of the
stopping criteria, see 基于监视器的属性.