The
Material Law Models define the relationship between stress and strain in the solid material.
Simcenter STAR-CCM+ supports linear elastic materials and elastoplastic materials with either isotropic, orthotropic, or anisotropic properties, and isotropic hyperelastic materials.
Model Controls (Child Nodes)
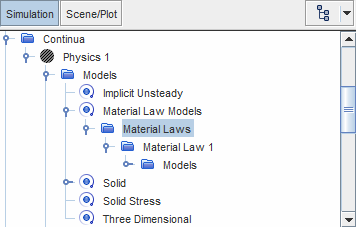
- Material Laws
-
- Allows you to create the material laws that define the stress-strain relationship in solid materials. When you right-click the
Material Laws node and select
New,
Simcenter STAR-CCM+ creates a material law with the default name
[Material Law 1].
-
-
- Allows you to select the
physics models that define the material law. The available
models are:
Material Stiffness Models |
Material Strain Measures |
Material Models |
- Linear
Elasticity
- Defines a linear elastic stress-strain
relationship for the material (Eqn. (4503)).
- This model cannot be used if you have
selected both the Nearly Incompressible
Material and Nonlinear
Geometry models in the solid physics
continuum. In this case, select the
Hyperelasticity model.
|
- Linear Strain (Small
Strain)
- Defines the material strain using Eqn. (4444).
- Green-Lagrange (Small
Strain)
- Defines the material strain using
Eqn. (4445). Only
available when the Nonlinear
Geometry model is activated.
|
- Isotropic Linear
Elastic
- Defines the material as isotropic (see Eqn. (4511)). The mechanical properties of
isotropic materials are the same in all
directions. See Material Properties.
- Orthotropic Linear
Elastic
- Defines the material as orthotropic (see Eqn. (4505)). The mechanical properties of
orthotropic materials are specified independently
along three mutually-orthogonal directions.
- Anisotropic Linear
Elastic
- Defines the material as anisotropic (see Eqn. (4504)). The mechanical properties of
anisotropic materials depend on direction.
|
- Hyperelasticity
- Defines a nonlinear hyperelastic stress-strain
relationship in terms of the strain energy
potential (Eqn. (4529)).
|
- Green-Lagrange (Large Strain)
- Defines the material strain using Eqn. (4446).
|
- Neo-Hookean
- Uses a Neo-Hookean strain energy potential (see
Eqn. (4533)). This model is the simplest
hyperelastic model and is suitable for strains
<20%. Use this model when the available
material test data are not sufficient for a
Mooney-Rivlin or
Ogden approach.
- Mooney-Rivlin
- Uses either a 2-term, 5-term, or 9-term
Mooney-Rivlin potential (see Eqn. (4535)). This model requires accurate
material test data.
- Ogden
- Uses an Ogden strain energy potential (see Eqn. (4539)) up to the 6th order. This model
is suitable for very large strains and requires
accurate material test data.
|
-
-
Optional Models |
Material Models |
- Plasticity
- Accounts for the plastic deformation that occurs
for stresses above the yield stress.
- Available when you activate the Linear
Elasticity model.
|
- J2 Plasticity
- Models plastic yield using the von Mises
potential model. For more information, see Elastoplastic Materials.
|
- Thermal
Expansion
- Accounts for the thermal strain due to
temperature loads (see Eqn. (4452).
|
- Isotropic Thermal
Expansion
- Use
this option for materials in which the coefficient
of thermal expansion is the same in all
directions. See Material Properties. For hyperelastic
materials, this is the only available option.
- Orthotropic Thermal
Expansion
- Use
this option for materials in which the coefficient
of thermal expansion is different along three
mutually-orthogonal directions.
- Anisotropic Thermal
Expansion
- Use
this option when the coefficient of thermal
expansion depends on direction generally.
|
Material Properties
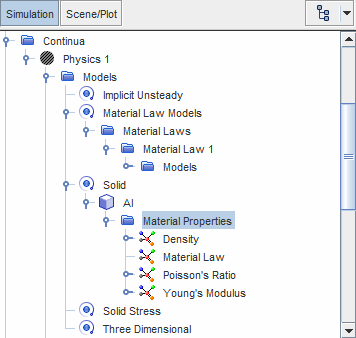
- Common Properties
- The following material properties are available for all solid materials, regardless of the material law models in use:
- Material Law
- The Type property allows you to select a material law
from the material laws under the node. See Model Controls.
- Anisotropic material laws also require you to specify the material law orientation for
each region associated with the anisotropic law. For more
information, see Material Law Orientation.
- Density
- Defines the mass per unit volume in the undeformed state ( in
Eqn. (4456)).
- Mechanical Properties
- When you set the
Material Law property,
Simcenter STAR-CCM+ adds mechanical properties based on the stiffness models that define the material law.
-
表 1. Linear
Elasticity
Material
Law Models |
Material
Properties |
Isotropic Linear Elastic
|
- Poisson's
Ratio
- Defines Poisson's ratio (
in Eqn. (4513)).
- Young's
Modulus
- Defines the Young's modulus
(
in Eqn. (4513)).
|
Orthotropic Linear Elastic
|
-
- The
nodes nu12,
nu23, and
nu13 define the Poisson
coefficients of the orthotropic material
(
,
,
in Eqn. (4506) and Eqn. (4507)).
-
- The
nodes E1,
E2, and
E3 define the Young modulus
coefficients of the orthotropic material
(
,
,
in Eqn. (4506) and Eqn. (4507)).
-
- The
nodes G1,
G2, and
G3 define the shear modulus
coefficients of the orthotropic material
(
,
, and
in Eqn. (4505)).
|
Anisotropic Linear Elastic
|
- Anisotropic Stiffness
Coefficients
- These define the independent components
of the material
tangent
(see Eqn. (4504)).
|
-
表 2. Plasticity
Material Law Models
|
Material Properties
|
J2 Plasticity
|
- Plastic Yield Stress
- The
Method property allows you to specify the hardening model that describes the plastic portion of the stress-strain curve. The available options are:
- Linear Isotropic Hardening—the yield stress is a linear function of the plastic strain (see
Eqn. (4523)). Set the coefficients
sigmaY and
H0 ( and in
Eqn. (4523)) under the
node.
- Saturation Hardening—the yield stress is a nonlinear function of the plastic strain (see
Eqn. (4524)). Set the coefficients
sigmaY_0,
sigmaY_inf,
m,
H_bar, and
delta (, , , , and in
Eqn. (4524)) under the
node.
- User-Defined—the stress-strain curve is defined by the yield stress and its derivative with respect to the plastic strain (see
Eqn. (4525)). Set
sigma_Y and
d(sigma_Y) under the
node.
|
-
表 3. Hyperelasticity
Material
Law Models |
Material
Properties |
Mooney-Rivlin
|
- Bulk
Modulus
-
Defines the initial bulk modulus
in Eqn. (4535).
- Mooney-Rivlin Material
Parameters
- Define the coefficients
of the Mooney-Rivlin
potential (see Eqn. (4535)). The number of coefficients
depends on the number of terms of the polynomial
that approximates the potential. See Eqn. (4536) (2-term model), Eqn. (4537) (5-term model), and Eqn. (4538) (9-term model).
|
Ogden
|
- Ogden Material
Parameters [i]
- Allows you to specify the parameters that define
each term of the Ogden potential (Eqn. (4539)). That is:
|
Neo-Hookean
|
- Bulk
Modulus
- Defines the initial bulk
modulus
in Eqn. (4533). The Bulk Modulus must be
positive (> 0).
- Neo-Hookean Material
Parameters
- Specifies the
coefficient
in the Neo-Hookean
potential (see Eqn. (4534)). The Neo-Hookean Material
Parameters must be positive (> 0).
- Poisson's
Ratio
- Defines the initial Poisson's ratio,
(see Eqn. (4513)
andEqn. (4534)). The
Poisson's Ratio must be between -1 and 0.5.
- Young's
Modulus
- Defines the initial Young's modulus,
(see Eqn. (4513)
andEqn. (4534)). The
Young's Modulus must be positive (> 0).
|
- Thermal Properties
-
- When the material law contains thermal expansion models,
Simcenter STAR-CCM+ adds thermal properties that define the behavior of the solid material in response to temperature changes.
-
Material Law Models
|
Material Properties
|
All thermal expansion models
|
- Zero Thermal Strain Reference Temperature
- Defines the reference temperature at which the thermal strain is zero ( in
Eqn. (4452)).
|
Isotropic Thermal Expansion
|
- Thermal Expansion Coefficient
- Defines in
Eqn. (4452).
|
Orthotropic Thermal Expansion
|
- Orthotropic Thermal Expansion Coefficients
- Defines the components , , in
Eqn. (4510).
|
Anisotropic Thermal Expansion
|
- Anisotropic Thermal Expansion Coefficients
- Defines the components in
Eqn. (4504).
|
Material Law Orientation
When selecting non-isotropic material law
models, you define most material properties as second-order tensors (see Tensor
Quantities). You define the tensor components in a local coordinate
system, which is specified at the region level using the node. For more information, see Orientation Manager and Local Orientations.
Field Functions
- Common Field Functions:
-
- Material Basis
Vector 1, Material Basis Vector
2, Material Basis Vector 3
- Vector field functions that represent the
basis vectors of the coordinate system with respect to which the
material properties are defined. See Material Law Orientation.
- [Material
Property]
- Each material property is stored in a
field function with the same name.
For
orthotropic and anisotropic material properties, which are
defined by several coefficients, Simcenter STAR-CCM+ creates a field function
for each coefficient. In field function selection dialogs,
Simcenter STAR-CCM+
organizes the coefficient field functions into groups. For
example, the anisotropic thermal expansion coefficient field
functions are grouped under Anisotropic Thermal
Expansion.
- Plasticity Field Functions:
- The following field functions are available when the
Plasticity model is active:
- Equivalent Plastic
Strain
- Represents a
scalar measure for the plastic strain that is accumulated as the
plastic deformation increases (see Eqn. (4518)).
- Effective Plastic
Strain
- Represents a
scalar measure for the plastic strain (see Eqn. (4519)).
- Plastic Strain
Energy Density
- Represents the
energy that is dissipated due to plastic deformation (see Eqn. (4517)).
- Plastic Strain
Tensor
-
in Eqn. (4515).
- Thermal Expansion Field Functions:
- The following field functions are available when one of the
Thermal Expansion models is active:
- Thermal Strain
Tensor
- Represents the thermal strain tensor in Eqn. (4452).
注 | When you map
temperature data from a different mesh representation of the solid, for
example, a FV solid region in a Simcenter STAR-CCM+ CHT analysis, the mapping operation generates a
field function with the default name,
MappedVertexTemperature. See Applying Thermal Loads.
|