Volume Mesher Controls and Values
This section details the common controls, values, and right-click actions for all volume meshers. Controls that are specific to one mesher are detailed in the reference section for that mesher.
If you remove a volume mesher from an Automated Mesh operation, Simcenter STAR-CCM+ saves any user-defined settings and restores them if you reactivate the volume mesher.
Common Properties
- Field Function Based Refinement
- Specifies the field function for Field Function Mesh Refinement, which are based upon an existing solution. This option is not available for the thin mesher.
- Run Post Mesh Optimizer
- When activated, runs a vertex-based optimizer on the assembled mesh to fix low quality cells which are below the remediated cell quality threshold for any combination of meshers. The optimizer also moves internal vertices in the volume mesh to improve the mesh metrics. See Mesh Quality. In some cases, the optimizer can have an adverse effect on cells which are above the cell quality threshold. This option is activated by default, and although this property incurs an additional CPU overhead, you do not generally deactivate it.
- Quad Input Surface Conformality
- When activated, the volume mesh boundary matches the remeshed input surface. This option is visible only when the Meshing Method for the Surface Remesher is set to Quad Dominant. The Quad Input Surface Conformality property is available for the Polyhedral Mesher when you use it in combination with the Prism Layer Mesheror Thin Mesher, and a Quad Dominant surface mesh.
- Conformal To Existing Mesh
- When activated, generates a conformal mesh with another part in a different Automated Mesh Operation using the Tetrahedral core volume mesher.
Core Mesh Optimization Properties
- Optimization Cycles
- Specifies the number of optimization cycles that the mesher runs on the tetrahedral mesh (or, in the case of a polyhedral mesh, on the initial tetrahedral mesh before generating polyhedral cells). The recommended range is between 1 (lowest quality) and 3 (highest quality).
- Quality Threshold
- Specifies the target mesh quality. Use this property with the Optimization Cycles to improve mesh quality. The recommended range is between 0.4 (lowest quality) and 0.6 (highest quality). Increasing the quality also increases the meshing time.
注 | Both the Optimization Cycles and Quality Threshold are not available for the trimmed cell mesher. |
Post Mesh Optimization Properties
- Optimize Boundary Vertices
- When activated, the optimizer moves vertices on mesh boundaries to improve the mesh quality. By activating this property, the probability of fixing low quality cells attached to the boundary is increased. This results in fewer remediated cells near the boundary.
- Optimize Cell Topology
- When activated, the optimizer helps prevent formation of cells that would cause the solution to diverge. In particular, if a flow region has narrow passages where prism layers retract (because there is not enough space for prisms) the remaining core cells could span boundaries. As it is not possible to compute gradients on these cells, the cell topology optimization feature splits these cells. This option is only available for the trimmed cell and polyhedral meshers.
Volume Growth Rate
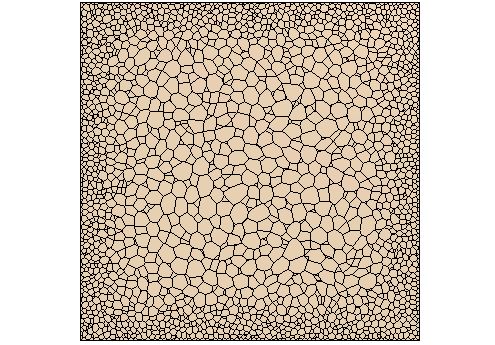
- Volume Growth Rate
- This property defines the growth of the mesh size. This value should be set to between 1.0 and 2.0. An expansion rate of 1.0 is associated with a mesh that has uniform density throughout the assigned region. Increasing the growth factor increases the rate at which cell sizes grow with distance away from the boundary, up to the limit set by the Maximum Cell Size.
Conformal Contacts Properties
- Contacts
- Allows you to select the part surface contacts. This property is available only when Conformal To Existing Mesh is activated in the Tetrahedral Mesher node.
Maximum Tet Size
The Maximum Tet Size node limits the largest cell size permitted anywhere in the domain.
For a polyhedral mesh, the value that you set here is applied to the underlying tetrahedral mesh that the polyhedral mesher initially generates. The tetrahedral mesh is then converted to a polyhedral mesh during dualization. For this reason, the maximum cell size limit does not apply directly to the polyhedral mesh; however, it indirectly affects the cell size through the intermediate tetrahedral mesh.
- Maximum Cell Size
- For the trimmed cell mesher, this parameter controls the maximum allowable cell size in the template refinement scheme when used with the trimmer. Selecting the Size Type property governs which of the two entry options for the value is activated, Relative to Base or Absolute.
- Size Type
- Allows you to define the maximum cell size either as an Absolute value or as a percentage Relative to Base.
零部件优先级
- 排序条件
- 用于在并发执行网格化时区分部件的优先级。为此有四个选项可供选择:
- 默认 - 部件按创建顺序进行排序。
- 表面积 - 部件按表面积从大到小的顺序网格化。表面积根据每个部件的根描述计算得出。
- 体积 - 部件按体积从大到小的顺序网格化。体积根据每个部件的根描述计算得出。使用的是体积的绝对值,因此开放体积和负体积部件会影响顺序,并且列出这些部件的“输出”窗口中会输出伴随的错误。
- 手动 - 可使用“优先级集合”对部件进行分类。部件按优先级集合的索引进行排序(可重新排序)。优先级集合内的所有零部件按其创建顺序进行排序。不在任何优先级集合中的零部件的优先级最低,同样也按创建顺序进行排序。此选项可用于优先计算昂贵的零部件。“输出”窗口将显示网格化过程中每个零部件的计算时间。
Common Right-Click Actions
- Restore Default Settings
- Allows you to restore all properties to the default value.