Smoothed-Particle Hydrodynamics (SPH): Gearbox Lubrication
Gear mechanisms require adequate lubrication for long-term optimum performance and efficiency. Simcenter STAR-CCM+ provides the Smoothed-Particle Hydrodynamics (SPH) model with which you can simulate the flow of lubricant around the parts of a gear mechanism and determine whether adjustments are necessary.
SPH is a meshfree method that uses a Lagrangian particle-based approach to simulate fluid dynamics. This numerical method overcomes meshing related constraints that occur with traditional models and is particularly useful for simulating fast dynamic and complex flows with moving parts.
The focus of this tutorial is on demonstrating the workflow for setting up an SPH simulation to predict the flow field, the wetting of the gears, and the gear torque in a gearbox.
In the first part of the tutorial, you simulate an oil bath lubrication system where the gears are partially immersed in the lubricant. This lubrication method is commonly used for low-speed operation. In the second part, you simulate the lubrication of the gearbox using oil injection, which is the preferred method for high-speed applications. Due to the rotation of the gears, both methods form a lubrication film on the teeth of the gears.
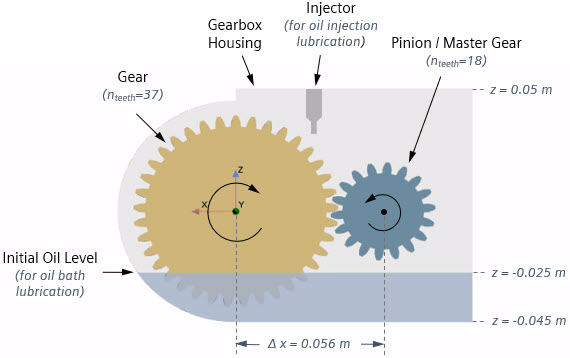
For the oil bath lubrication simulation, the gearbox forms a closed system containing no flow boundaries. The interlocking gear and pinion sit in an oil bath and counter-rotate at low speed. The pinion rotates at a rate of 1222 rpm and the large gear rotates at a rate of -594.5 rpm. At the beginning of the simulation, the oil level in the housing is 0.02 m. The oil is discretized by fixed-size particles with a diameter of 1 mm. The simulation stops at a physical time of 0.5 s.
For the simulation of oil injection lubrication, an injector at the top of the gearbox introduces oil particles into the system. The injector has an inlet diameter of 2 mm and injects the oil with a mass flow rate of 0.06 kg/s. The diameter of the injected oil particles is 0.3 mm. The pinion spins at high speed with a rotation rate of 12000 rpm and the large gear rotates at a rate of -5837.8 rpm. The simulation stops at 0.01s.
The oil is modeled as an incompressible liquid with a density of 845.1 kg/m^3 and a dynamic viscosity of 0.074 Pas. You run the simulation using adaptive time-stepping, which dynamically adapts the time-step size based on the mesh size and the computed velocities.