Mapped Contact Interface
The Mapped Contact Interface is an indirect interface type between fluid/solid and solid/solid boundaries that allows for a non-conformal mesh.
This interface type is a variation of contact interface type applicable to indirect interfaces. The mapped contact interface relies on an indirect association between faces of the interfacing boundaries, for data mappers, rather than the imprinted connection used for direct interfaces.
The Mapped Contact Interface is created on the volume meshes generated by the meshing process. When the interface is created from two boundaries, two new interface boundaries are automatically added. The original boundaries from which the interface is created are not destroyed.
Each face of the original boundary is linked with a group of faces on the opposing boundary using a proximity-based algorithm. Once the associativity of all the faces on the original boundary has been processed, the faces are split into an associated face-set and a disassociated face-set.
The associated face-set is transferred on to the interface boundary, while the unassociated face-set is retained on the original boundary. This is analogous to the creation of a direct interface, except that this process does not result in any new faces.
The main advantage of a Mapped Contact Interface is that it allows for a non-conformal mesh across the interface. This type of mesh is desirable in cases where the interfacing boundaries have different mesh resolutions. For instance, the heat conduction in the solid region requires a coarser mesh compared to resolving the boundary layer in the fluid domain. By precluding the need for imprinting, this approach retains the high quality of the originally created mesh and also reduces the resultant face count. A co-product of this approach is better accuracy in computing the face gradients as well as better quality mesh for visualization. This approach is also better suited for cases where the geometric features are not equally resolved on either side of the interface. While imprinting may leave more non-intersected faces, this technique can find an associated face on the opposing boundary more robustly.
When a boundary of a Mapped Contact Interface is attached to a region for which the overset method is applied, the data across the interface is only exchanged between active cell faces and the boundary faces on the other side of the interface. A boundary cell face is considered active when its associated cell is an active cell. The inactive cells of the overset region do not participate in the interface data exchange.
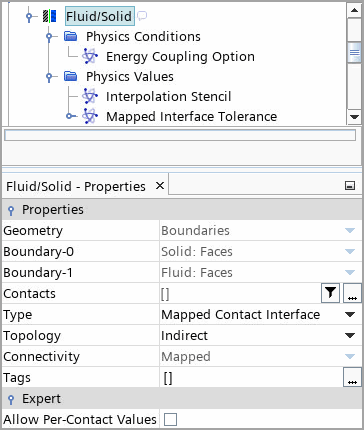
Mapped Contact Interface Properties
You can use the properties that are listed below to adjust the specifications of a Mapped Contact Interface node.
- Boundary-0
- Indicates the "fixed" side of the interface (Read Only).
- Boundary-1
- Indicates the "adapted" side
of the interface (Read Only).
Vertices from boundary-1 are projected onto boundary-0. The orientation can be swapped through the right-click action Reverse Orientation.
- Type
- Defines the type of interface. Must be set to Mapped Contact Interface.
- Topology
- Defines the connection type between the interfaces. Only the Indirect type is possible.
- Connectivity
- Defines how the boundaries on two sides of the interface are connected. Only Mapped connectivity is possible.
Mapped Contact Interface Conditions
The following physics conditions depend on the physics models that are active in the physics continua.
- Energy Coupling Option
- Specifies implicit or explicit coupling of the energy equation across the interface. Implicit is the default. The Explicit option results in the mapping of thermal fields across the two interface boundaries. The Explicit method for the Energy Coupling Option is available only when the interface connects a fluid and a solid region. See Explicit Energy Coupling Thermal Boundary Conditions.
- Energy Source Option
- Provides energy source options for the interface.
- None—Do not specify an energy source.
- Heat Flux—Specifies a user-defined heat flux in W/m2.
- Heat Source—Specifies a user-defined heat source in W.
- Mechanical Interaction
- Specifies the type of contact between the two solid regions.
- Bonded—The contacting surfaces undergo continuous displacements. If the solid regions are different materials, discontinuities in the strain are preserved across the material interface.
- Small Sliding Frictionless—The contacting surfaces are free to slide over each other, however movement is prohibited normal to the interface. The shear stress at the contact interface is equal to zero, and the normal forces are equal and opposite.
Explicit Energy Coupling Thermal Boundary Conditions
When the Energy Coupling Option is set to Explicit, the following conditions apply on the two interface boundaries:
- Fluid interface boundary: Temperature thermal boundary condition
- Solid interface boundary: Convection thermal boundary condition
Find each at
.- Explicit Energy Coupling Thermal Boundary Physics Values
- The following boundary physics values are set automatically according to the Time Averaging Option selection for the solid interface boundary (for Ambient Temperature and Heat Transfer Coefficient) or the fluid interface boundary (for Static Temperature). The profile methods map the corresponding values from the interface boundary on the other side of the interface to this interface boundary.
Mapped Contact Interface Values
- Mapped Interface Tolerance
- Activates the search algorithm and specifies tolerances that the algorithm uses to find the neighbors to the cells.
- Proximity Check—When activated, the minimum proximity check occurs.
- Minimum Proximity—The relative distance (based on cell size) to the target cell. 1 is equivalent to 100%.
- Normal Directions check—When activated, the normal direction check occurs.
- Minimum Angle—The angle, in degrees, between the source and target face normals. When the minimum angle is 0, the two normals point in the same direction, when 180, the normals point toward each other.
- Contact Resistance
- The value of the
resistance to conduction through the interface. It is entered as a
scalar profile. If a field function defines the value and the Ignore Boundary Values property on the field function is activated, the function is computed using data from the cell next to the boundary identified by the Boundary-0 property of the interface.
- Dimensions—specify
the resistance in units of
or similar. Read Only. - Method—specify the input method type from Constant, Field Function, Table, or User Code.
- Dimensions—specify
the resistance in units of
- Heat Flux
- Specifies the heat
transferred per unit area. It is activated when the Energy
Source Option is set to Heat
Flux.
- Dimensions—specify the heat flux in units of W/m2 or similar. Read only.
- Method—specify the input method type from Constant, Field Function, Table, or User Code.
- Heat Source
- Specifies the heat
transferred. It is activated when the Energy Source
Option is set to Heat Source.
- Dimensions—Specify the heat source in units of W or similar. Read only.
- Method—Specify the input method type from Constant, Field Function, Table, or User Code.
- Interpolation Stencil
- Specifies the method that Simcenter STAR-CCM+ uses for connecting
the mesh faces on the two sides of the interface:
- Compact—This scheme builds a connectivity map by finding the nearest neighbor of a face on the opposite side of the interface. The scheme includes a symmetry specification step which can add extra faces to the stencil (that is, if a face on boundary 0 sees a face on boundary 1, then the face on boundary 1 will also see the face on boundary 0). After the connectivity map is created, face area ratios are used to define the interpolation weights.
- Imprint—This scheme builds a connectivity map by finding all the faces on the opposite side of the interfaces that overlap with a face.
Compared to the Compact method, the Imprint method results in better connectivity that leads to more accurate enforcement of physics conditions at the interface. However, the Compact stencil is more tolerant to mesh irregularities, whereas the imprint process can fail in the case of poor quality meshes.
Field Functions
Mapped contact interfaces activate field functions that allow you to assess the quality of intersection at the interface:
- Mapped Facet Count
- Indicates how many faces of the opposing boundary are identified as connections. Available for all boundaries that participate in a mapped interface. For a mapped interface boundary, you can visualize the total number of connections by selecting the corresponding boundary node under .
- Mapped Facet Area Match
- Indicates the ratio between the sum of overlap areas of the partner faces and the area of the current face. A value close to 1.0 indicates that interface initialization was effective. The value can deviate largely from 1.0 for partially overlapping faces.