Surrogates: Reliability of an Industrial Exhaust System
Robustness and reliability studies are employed to assess the influence of installation and manufacturing tolerances on the performance of a design. In Design Manager, surrogate models provide an efficient method for running these studies as using surrogates reduces the overall number of flow simulations that must be run.
Surrogate models, also known as response surface models (RSM), allow you to capture the response of a system to its inputs in a form that can be queried by other computations in separate studies. For this reason, surrogate models are appropriate when performing robustness studies as these studies cover a large number of permutations around a chosen design. Running full simulations for each permutation is expensive.
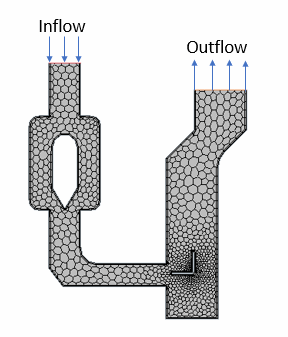
Flow enters the left channel of the exhaust manifold with a velocity of 9.1 m/s. In the right channel, the flow is deflected by a turning vane before it leaves the domain. Several elements of the geometry are parametrized. These geometric parameters are varied during the Design Manager studies.
- Optimization study—to find the best design for the exhaust manifold, the geometric input parameters are varied with the objective of minimizing the pressure drop between inflow and outflow. The solution is constrained by the requirement that the velocity uniformity at the outlet be at least 87%.
- Adaptive sampling study—to compute surrogate models for pressure drop and velocity uniformity, you perform a local exploration around the best design using Adaptive Strategy Balance Local and Global Accuracy. The design space for this study is evenly distributed. To assess the accuracy of the surrogate models, you perform cross validations. At the end of the study run, surrogate models are automatically generated with the most appropriate surrogate settings.
- Robustness and reliability study—using the previously generated surrogate models for pressure drop and uniformity, you investigate the impact of small variations on input parameters. In real life these would come from manufacturing tolerances or deviations in the installed location.